Says: | Sławomir Kiszycki, CFO, Deputy President of the Management Board, Unibep Leszek Gołąbiecki, President of the Management Board, Unibep |
Modular construction is becoming popular in Poland. This popularity is driven by the growing prices of building materials and labour shortages
Modular construction is no longer associated with temporary buildings. This method can be used to build homes as well as hotels, public housing, and educational establishments. And, what is important, it is much cheaper and faster than traditional construction technologies. This growth in the popularity of modular construction in Poland can be driven by the recent increase in the prices of building materials and labour shortages, both of which have translated into generally higher prices in the construction industry.
“Modular construction is characterised by competitive prices and speed. You can have the modules produced and assembled on site within six months. This can become an alternative to traditional construction, just as was the case a few dozen years ago in Scandinavia. Such buildings can serve various purposes, such as hotels or homes, in which case they are constructed like standard development projects,” Sławomir Kiszycki, CFO and Deputy President of the Management Board of Unibep told Newseria Biznes in an interview.
Prefabricated modules are no longer associated with temporary buildings, such as metal technical or exhibition containers. Now this technology is also used to build homes, hotels, and even kindergartens and schools.
“In Sweden, we have constructed some buildings that were originally intended for refugees, but eventually the local commune, which was our client, made them available for young couples, who had only recently got married. We also constructed halls of residence. In Poland, too, we can build halls of residence, hotels or residential buildings – it is all a matter of design and visualisation, and we’re ready to go,” says Sławomir Kiszycki.
Modular construction offers many benefits, hence its growing popularity in such regions as Scandinavia and the United States. This technology is based on producing modules in a factory and then delivering them to the construction site to be connected to the underground infrastructure. Individual modules can be joined to make larger buildings. Compared to traditional construction technologies, this method is much faster and more cost-effective.
“During the previous year we produced 990 modules. This year we expect this figure to reach 1,300. We have almost completed the development of our factory, which will increase our production capacity to 2,000 items. So far, our modules have been exported mainly to Norway, and since 2017 also to Sweden. This technology is well-known in Scandinavia. But the prospects for using modules and economic buildings in Poland are also exciting,” says Sławomir Kiszycki.
The Deputy President of Unibep believes that the popularity of modular buildings in Poland can grow as a result of the increase in traditional construction prices, which could be noticed especially in the second half of the previous year and was driven by the growing prices of subcontractor services and materials, and labour shortages.
Export accounts for a significant part of Unibep’s revenue – in the recent years it was more than 20%. The company exports its products mainly to Scandinavia, including Sweden and Norway, which are the main recipients of the modular buildings produced in its plant in Bielsk Podlaski. Unibep has also long been present on eastern markets, especially in Belarus and Russia, where it engages in various projects.
Modular construction can be the response to what has been happening on the Polish market, especially in the second half of 2017, including noticeable increases in the prices of subcontractor services and materials, as well as labour shortages. Modular construction can offer competitive prices within a year or two, in our estimation. And secondly, it is fast. We are able to produce and assemble modules on site within six months. We believe this can become an alternative to traditional construction, just as was the case a few dozen years ago in Scandinavia. Modular construction was developed in Scandinavia.
We export mainly to Scandinavian markets, where the modular products from our factory in Bielsk Podlaski are marketed. And we have a long presence on eastern markets, such as Russia, Belarus, and Ukraine. This is where we’re implementing our projects, especially commercial facilities. Previously, we built hotels and offices in Russia. Now, we’re building a shopping centre, a logistics hub, and a tennis centre. We are also present in Ukraine, where we have recently signed an EUR 66 m contract for the development of the border crossing in Shehyni. This contract includes Polish companies only and is based on a credit agreement concluded between the Polish and Ukrainian governments to improve road infrastructure.
All our projects in Belarus, including the shopping mall in Grodno and the tennis centre in Minsk, rely on financing provided by a Polish bank, BKG. BGK has extended a credit to a Belarussian bank which is financing the project, and all this is insured in KUKE. This financing is very favourable for the Ukrainians and is based on very low interest rates, but the condition is that the project can only be implemented by a Polish company.
Read also
- 2025-05-30: UE dąży do większej samodzielności w dostępie do surowców krytycznych. Częściowo pozyska je z recyklingu baterii
- 2025-04-04: W drugiej połowie roku do sprzedaży trafi najinteligentniejszy Mercedes. W pełni elektryczny CLA jest krokiem do całkowitej dekarbonizacji produkcji
- 2024-11-13: Dekarbonizacja jest wyzwaniem dla firm przemysłowych. Wymaga zmian w całym łańcuchu dostaw
- 2019-10-23: Przemysł 4.0 zrewolucjonizuje gospodarkę, zwłaszcza w segmencie automotive. Brak wdrożenia innowacyjnych linii technologicznych może skutkować wypadnięciem z rynku
- 2018-10-21: Polish defence industry exhibits a significant growth potential. Polish army equipment tenders open huge prospects to companies.
- 2018-06-14: The number of investments in energy-saving solutions is increasing. The related risks can be taken over by specialised companies.
- 2018-05-21: A new concept by Volvo in central Warsaw. This is a first car dealership in the world with a coffee house and a cultural centre.
- 2018-05-09: Towns and cities are in want of innovative solutions for fighting smog. They are looking for start-ups which could deliver such technology.
- 2018-05-11: As many as a million Poles are cooperating with the direct sales sector. Customers usually buy dietary supplements and home appliances.
- 2018-05-15: Na popularności zyskuje budownictwo modułowe. To efekt rosnących cen materiałów budowlanych i braku rąk do pracy
Trade
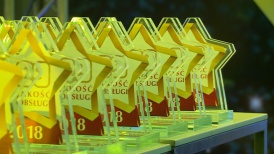
Polish consumers are more satisfied than Americans, with the customer satisfaction level being close to 80 percent
For six years the customer satisfaction index in Poland has grown by over 17 percentage points to nearly 78 percent, and it currently exceeds the customer satisfaction levels recorded in the USA and the United Kingdom. Service quality and its growing significance among businesses have had a tremendous impact on customer satisfaction. For the eleventh time the Customer Service Quality Star titles have been awarded to entrepreneurs recording the best results in this field.